In the ever – evolving landscape of workplace safety, a silent revolution is underway, driven by the advent of revolutionary portable gas sensors. These compact yet powerful devices are reshaping the way safety assessments are conducted across a wide range of industries, from oil and gas to mining, manufacturing, and construction. By providing real – time, accurate, and reliable gas detection capabilities, they are enhancing worker safety, preventing accidents, and ensuring compliance with stringent safety regulations.
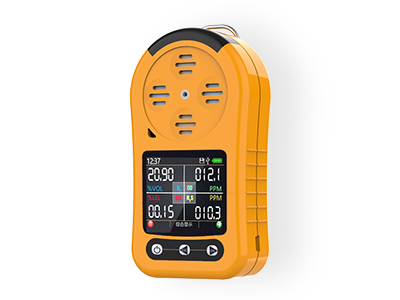
The Need for Enhanced Workplace Gas Safety
Workplaces are often fraught with potential gas – related hazards. In the oil and gas industry, for example, workers are exposed to a variety of toxic and flammable gases such as hydrogen sulfide (H₂S), methane (CH₄), and volatile organic compounds (VOCs). H₂S, often referred to as “sour gas,” is highly toxic and can cause rapid unconsciousness and death even at low concentrations. Methane, on the other hand, is a highly flammable gas that can lead to explosive situations if it accumulates in confined spaces.
Mining operations also present significant gas risks. Underground mines can be filled with harmful gases like carbon monoxide (CO), which is produced by the incomplete combustion of materials, and carbon dioxide (CO₂), which can displace oxygen and lead to asphyxiation. Additionally, methane can seep into mines from coal seams, posing a constant threat of explosion.
Manufacturing facilities that deal with chemicals, solvents, and other substances are not immune to gas hazards either. VOCs released during various production processes can have long – term health effects on workers, including respiratory problems, neurological damage, and an increased risk of cancer. Construction sites, especially those involving welding, painting, or the use of adhesives, can also generate dangerous gases that require constant monitoring.
Traditional Gas Detection Methods and Their Limitations
Traditionally, gas detection in workplaces relied on fixed gas detection systems and manual sampling methods. Fixed systems, while effective in providing continuous monitoring in specific areas, had several drawbacks. They were often expensive to install and maintain, and their coverage was limited to the areas where they were installed. This meant that workers moving around the workplace or entering unmonitored areas were at risk of exposure to undetected gas hazards.
Manual sampling methods, on the other hand, were time – consuming and labor – intensive. Workers had to collect air samples using specialized equipment and send them to a laboratory for analysis. This process could take hours or even days, resulting in delayed detection of gas leaks or hazards. By the time the results were available, the situation could have escalated, putting workers’ lives in danger.
Moreover, both fixed systems and manual sampling methods lacked the flexibility and portability required to adapt to the dynamic nature of many workplaces. Workers often had to work in different locations within a facility or move between different job sites, making it difficult to ensure continuous gas monitoring.
The Rise of Revolutionary Portable Gas Sensors
Portable gas sensors have emerged as a game – changer in workplace gas safety assessments. These devices are compact, lightweight, and easy to carry, allowing workers to take them wherever they go. They are equipped with advanced sensors that can detect a wide range of gases with high sensitivity and accuracy.
Modern portable gas sensors use a variety of detection technologies, including electrochemical sensors, catalytic bead sensors, and infrared sensors. Electrochemical sensors are particularly effective at detecting toxic gases such as CO, H₂S, and NOₓ (nitrogen oxides). They work based on chemical reactions that occur when the target gas comes into contact with the sensor’s electrodes, generating an electrical signal proportional to the gas concentration.
Catalytic bead sensors, on the other hand, are commonly used for detecting flammable gases like methane and propane. These sensors rely on the catalytic combustion of the target gas on a heated bead, which causes a change in electrical resistance that can be measured to determine the gas concentration.
Infrared sensors are ideal for detecting gases that absorb infrared light, such as CO₂ and hydrocarbons. They offer high selectivity and stability, making them suitable for use in harsh industrial environments.
Real – Time Monitoring and Early Warning
One of the most significant advantages of portable gas sensors is their ability to provide real – time gas monitoring. Workers can carry these sensors with them as they perform their tasks, and the sensors will continuously monitor the air for the presence of dangerous gases. If a gas leak or hazard is detected, the sensor will immediately issue an alarm, alerting the worker to take appropriate action.
This real – time warning system is crucial for preventing accidents and saving lives. In the event of a gas leak, workers have only a limited amount of time to evacuate the area or take measures to mitigate the hazard. Portable gas sensors provide them with the early warning they need to react quickly and effectively, reducing the risk of injury or death.
For example, in a confined space such as a storage tank or a sewer, the accumulation of toxic or flammable gases can be extremely dangerous. A worker equipped with a portable gas sensor can detect the presence of these gases before they reach dangerous levels, allowing them to leave the area immediately and notify the appropriate authorities.
Enhanced Flexibility and Adaptability
Portable gas sensors offer unparalleled flexibility and adaptability in workplace safety assessments. They can be used in a variety of environments, from indoor facilities to outdoor job sites, and can be easily moved from one location to another as needed. This makes them ideal for industries where workers frequently change their work areas or move between different job sites.
In the construction industry, for instance, workers often work on different parts of a building site or move to new projects. Portable gas sensors can be taken with them to each location, ensuring continuous gas monitoring regardless of the work environment. Similarly, in the oil and gas industry, workers may need to inspect pipelines, wells, or offshore platforms. Portable gas sensors allow them to conduct safety assessments in these remote and challenging locations without the need for fixed gas detection systems.
Moreover, portable gas sensors can be customized to detect specific gases based on the requirements of a particular workplace. This means that industries with unique gas hazards, such as the semiconductor manufacturing industry, which uses a variety of toxic and corrosive gases, can have sensors tailored to their specific needs.
Data Logging and Analysis
Many modern portable gas sensors are equipped with data logging capabilities. This allows them to record gas concentration data over time, which can be later downloaded and analyzed. Data logging is a valuable tool for identifying trends, patterns, and potential sources of gas hazards in the workplace.
By analyzing the data, safety managers can determine the effectiveness of existing safety measures, identify areas where additional controls may be needed, and make informed decisions about workplace safety improvements. For example, if the data shows that gas concentrations are consistently higher in a particular area of a facility, it may indicate a problem with ventilation or a potential gas leak source that needs to be investigated.
In addition, data logging can be used for compliance purposes. Many safety regulations require companies to keep records of gas monitoring data to demonstrate that they are taking appropriate measures to protect workers’ health and safety. Portable gas sensors with data logging capabilities make it easy for companies to comply with these regulations and provide evidence of their safety efforts.
Training and User – Friendly Design
To ensure the effective use of portable gas sensors, manufacturers are focusing on user – friendly design and comprehensive training programs. Portable gas sensors are designed to be easy to operate, with intuitive interfaces and clear displays that show gas concentration levels and alarm status.
Training programs are also provided to educate workers on how to use the sensors correctly, interpret the data, and respond to alarms. This training is essential for ensuring that workers are confident and competent in using the sensors, and that they understand the importance of gas safety in the workplace.
Challenges and Future Directions
尽管便携式气体传感器有很多好处,但在工作场所广泛采用便携式气体传感器并非没有挑战。主要挑战之一是需要定期校准和维护,以确保传感器的准确性和可靠性。校准不当会导致误报或无法检测到实际的气体危害,从而可能造成严重后果。
另一个挑战是购买和维护这些传感器的成本。虽然近年来便携式气体传感器的价格有所下降,但对于一些公司,尤其是中小型企业来说,它们仍然是一项重大投资。
展望未来,便携式气体传感器需要进一步的技术进步。研究人员正在努力开发具有更高灵敏度、选择性和耐用性的传感器。人们也越来越关注将便携式气体传感器与其他安全技术(如个人防护设备 (PPE) 和可穿戴设备)集成,以便为工人创建更全面的安全解决方案。
总之,革命性的便携式气体传感器通过提供实时、准确和可靠的气体检测功能,正在改变工作场所的安全评估。他们正在提高工人安全、防止事故并确保遵守安全法规。虽然存在需要克服的挑战,但对这项技术的持续创新和投资将进一步改善工作场所的燃气安全,并保护所有行业工人的生命和健康。