Buying a Driving License: Risks, Regulations, and Realities
Introduction
In today's busy world, having a driving license is typically thought about a necessity. It provides flexibility of movement and is important for different job chances. Nevertheless, with the increasing demand for driving licenses, some people might think about the suspicious option of buying a license instead of going through the traditional procedure. This article seeks to explore the phenomenon of acquiring a driving license, highlighting the dangers involved, the policies governing driving licenses, and the ethical ramifications of such actions.
Comprehending the Driving License
A driving license functions as a legal file that grants a specific authorization to run a motor lorry. This license is usually issued by federal government authorities after a candidate meets particular requirements, including age, understanding of traffic guidelines, and successful conclusion of driving tests. Below are some essential points about driving licenses:
- Purpose: Ensures that only certified individuals can run cars safely.
- Types: Various types of licenses exist, including student's authorizations, complete licenses, and specialized licenses for various car types (e.g., industrial drivers).
- Regulatory Framework: Each country has its own laws and requirements governing the issuance of driving licenses.
The Allure of Buying a Driving License
While it is unlawful to buy a driving license, the appeal remains strong for some people. Various reasons may drive this decision, including:
- Lack of Time: For numerous, scheduling driving lessons and tests can be lengthy. Buying a license seems a fast option.
- Fear of Failure: The stress and anxiety related to screening can hinder some people from attempting to obtain a license through traditional ways.
- Monetary Constraints: In certain cases, people might think that purchasing a license is a more cost-effective option to paying for lessons and tests.
Despite these appealing reasons, it is vital to comprehend the more comprehensive ramifications of this option.
Threats Associated with Buying a Driving License
Legal Consequences
Getting a driving license is prohibited in the majority of nations and can result in major effects. Participating in this activity might lead to:
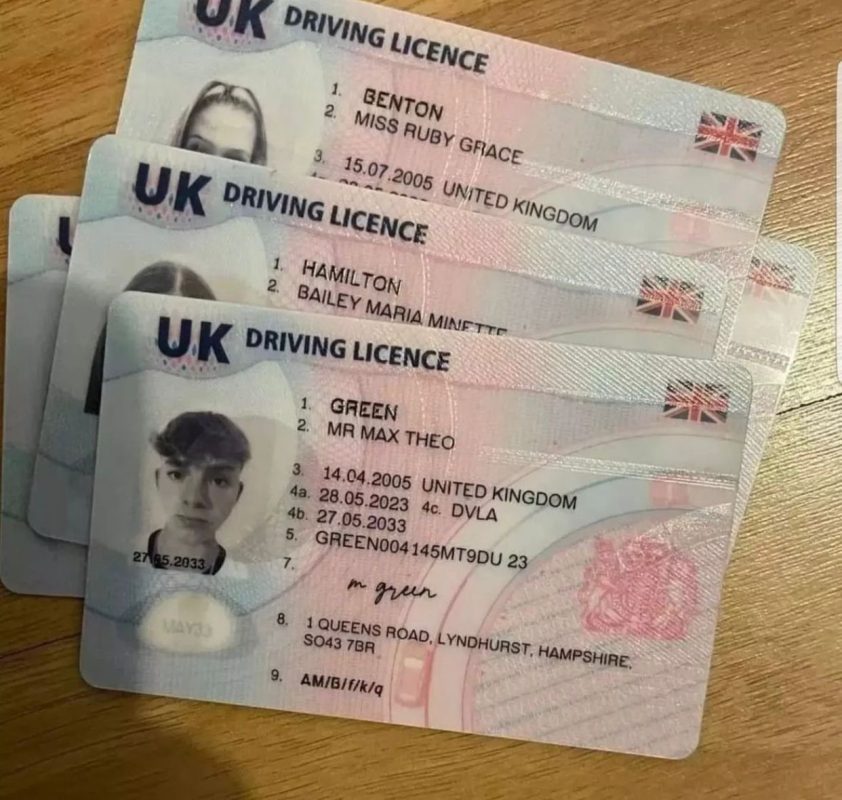
- Criminal Charges: Individuals captured buying a license might face fines or perhaps imprisonment.
- License Revocation: If authorities discover that a license was acquired fraudulently, it will be revoked right away.
Safety Concerns
Obtaining a license